Durability
Handle Design for User Comfort
The design of the handle plays a critical role in ensuring smooth operation and reducing strain during extended use. By focusing on ergonomics, it allows for a more comfortable grip, which is essential for maintaining control and precision. A well-crafted handle minimizes fatigue, enabling users to work for longer periods with ease.
Ergonomic Considerations
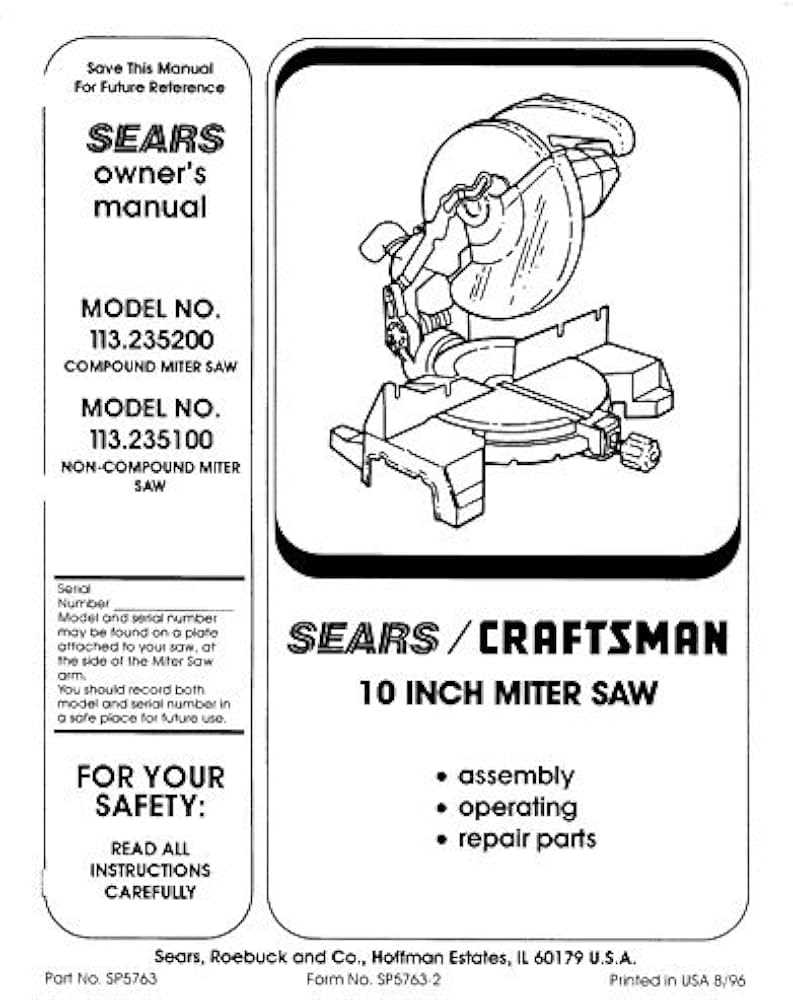
An ergonomic grip is essential to prevent discomfort and long-term injury. Handles shaped to fit the natural contours of the hand provide improved support, reducing stress on the wrist and forearm. These features contribute to a more stable and enjoyable experience for users, no matter the task at hand.
Material and Texture
The material and texture of the handle significantly affect comfort and control. Soft yet durable materials that offer non-slip surfaces ensure a firm grip even in varying conditions. This design choice prevents accidental slips and enhances user confidence, especially during extended
Trigger Switch Functionality and Maintenance
The functionality of a trigger mechanism is crucial for the operation of power tools, enabling users to control the tool’s activation with precision. This essential component is designed to provide a safe and efficient means of operation, allowing the user to start or stop the tool as needed. Understanding its mechanics is vital for both performance and safety.
Regular maintenance of the trigger switch is necessary to ensure its longevity and reliability. Dirt and debris can accumulate over time, leading to decreased responsiveness or malfunction. Periodically inspecting the trigger for signs of wear or damage, and cleaning it properly, can help prevent issues. If the switch becomes sticky or unresponsive, lubrication with appropriate substances may restore its function.
In case of persistent problems, replacing the trigger may be the best course of action. It’s important to consult the tool’s manual for specific instructions regarding disassembly and reassembly, ensuring that the new component is compatible. Proper installation is crucial to maintaining the tool’s overall safety and effectiveness.
Blade Guard Mechanism for Safety
The blade guard mechanism is a crucial safety feature designed to protect users from potential hazards during operation. This system functions to shield the cutting element when not in use, ensuring that accidental contact is minimized. A reliable guard mechanism contributes significantly to workplace safety, providing peace of mind while handling equipment.
Components of the Guard System
Understanding the essential components of the guard mechanism helps in recognizing its importance in safety practices. Key elements include:
- Guard Housing: The outer casing that encloses the cutting edge when the tool is not in use.
- Pivot Point: The hinge that allows the guard to move up and down, enabling clear visibility and access during operations.
- Spring Mechanism: This component ensures the guard returns to its closed position after use, offering continuous protection.
- Locking System: A feature that secures the guard in place during storage or transport, preventing unintended exposure.
Benefits of an Effective Guard Mechanism
Implementing a well-designed blade shield offers numerous advantages:
- Enhances user safety by minimizing the risk of accidental contact with the blade.
- Improves visibility and control during operation, allowing for more precise cuts.
- Reduces the likelihood of debris and particles being ejected, creating a cleaner work environment.
- Encourages best practices by reinforcing the importance of safety measures in the workspace.
In summary, a robust guard system is integral to safe tool operation. Understanding its components and benefits aids users in maintaining a safe working environment while enhancing their efficiency. Regular inspection and proper maintenance of this mechanism are essential to ensure its effectiveness.
Explaining the Miter Scale and Angle Adjustments
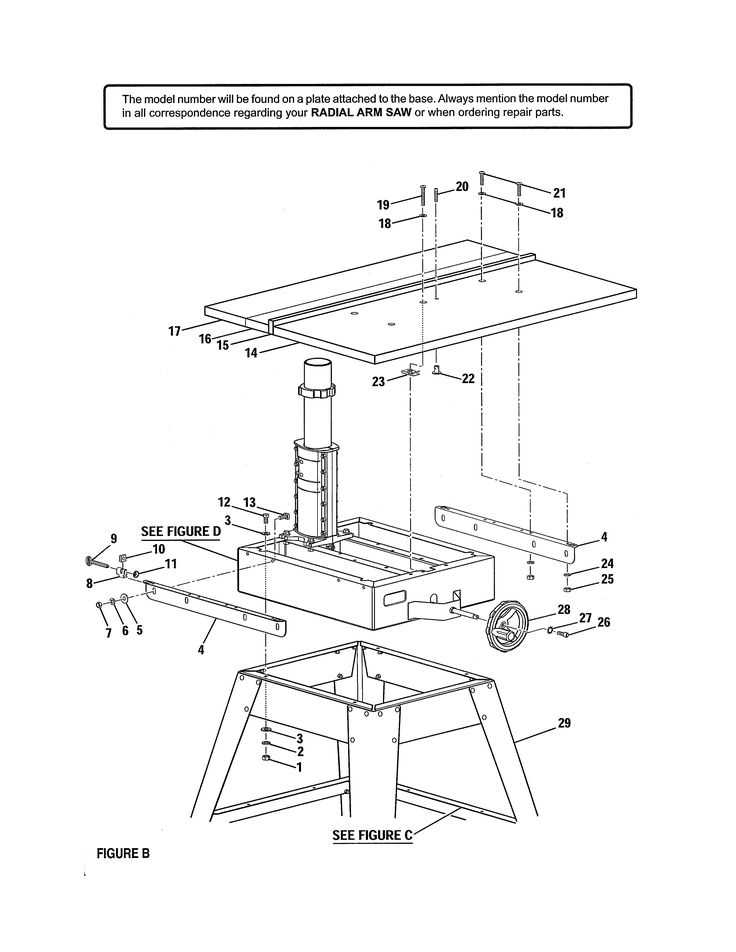
The precision of angled cuts is vital in woodworking, and understanding how to effectively utilize the scale and angle settings can significantly enhance the quality of your projects. This section delves into the intricacies of these adjustments, ensuring that users can make accurate modifications to achieve desired results.
The scale typically features markings that correspond to various angles, allowing users to quickly select the required setting. By aligning the cutting tool with these indicators, individuals can achieve consistent and repeatable cuts. It’s important to pay attention to both the primary and secondary scales, as they may offer different angle increments for more complex tasks.
Angle adjustments are usually facilitated through a locking mechanism that ensures stability during operation. Users should familiarize themselves with the adjustment knobs or levers that allow for smooth transitions between different angles. This adaptability is crucial for projects requiring precise bevel or compound cuts, where multiple angles are involved.
Maintaining accuracy involves regular calibration of the scale, as even minor misalignments can lead to significant discrepancies in finished pieces. It’s advisable to check the alignment against a known straight edge periodically, especially after extended use or transportation.
In summary, mastering the scale and angle adjustments not only improves the overall cutting experience but also elevates the craftsmanship in various woodworking endeavors. With practice and attention to detail, users can leverage these features to enhance their projects’ precision and quality.
Bevel System and Its Importance
The bevel mechanism is a crucial component in various cutting tools, allowing users to achieve angled cuts with precision. This feature enhances versatility and efficiency in projects requiring intricate designs and fitting components. Understanding its functionality can significantly improve the overall cutting experience and result.
Key Features of the Bevel Mechanism
- Angle Adjustment: Enables the user to set specific angles for accurate cuts.
- Locking Mechanism: Secures the angle, preventing accidental changes during operation.
- Ease of Use: Simplifies the process of making bevel cuts, making it accessible for users of all skill levels.
Benefits of Utilizing the Bevel System
- Improved Accuracy: Ensures cuts are made with greater precision, enhancing the quality of the finished product.
- Increased Versatility: Allows for a broader range of cuts, accommodating various project requirements.
- Enhanced Efficiency: Reduces the time spent on adjustments, enabling quicker project completion.
Dust Collection Features and Setup
Effective management of dust and debris is crucial for maintaining a clean workspace and ensuring the safety of the user. Various features and setups can enhance the efficiency of dust extraction systems, significantly reducing airborne particles and keeping the area tidy. Understanding the available options allows for optimal performance and ease of use.
Key Features of Dust Collection Systems
- Integrated Extraction Ports: Many models include built-in ports designed to connect with vacuum systems, enabling direct removal of sawdust as it is generated.
- Adjustable Chutes: Features that allow users to direct the flow of dust towards the collection system, improving overall suction efficiency.
- Filters and Bags: High-quality filtration systems help trap fine particles, while bags or containers can simplify the disposal process.
- Noise Reduction: Some setups are designed to minimize noise levels, making the workspace more pleasant while maintaining dust control.
Setting Up an Effective Dust Collection System
- Choose the Right Equipment: Select a dust collector that matches the specifications of your workspace and tools for optimal performance.
- Connect Properly: Ensure that all ports are securely connected to minimize leaks and enhance suction efficiency.
- Position Strategically: Place the collection system as close to the source of dust generation as possible to maximize effectiveness.
- Maintain Regularly: Regular cleaning and filter replacement are essential for sustaining performance and preventing clogs.
Locking Mechanisms for Precision Cuts
Achieving accurate and clean cuts requires reliable locking systems that stabilize the cutting tool during operation. These mechanisms play a crucial role in maintaining the desired angle and depth, ensuring consistency throughout the project. Understanding the various types of locking systems can greatly enhance the efficiency and precision of your cutting tasks.
Different types of locking mechanisms are designed to accommodate various cutting needs. Here are some commonly used systems:
- Quick-release clamps: These allow for fast adjustments and can be easily engaged or disengaged with one hand.
- Sliding locks: Often used to secure the tool in place, these locks provide added stability while working.
- Locking levers: Positioned for easy access, these levers help to secure the cutting angle firmly.
- Ratcheting systems: These provide precise adjustments and can be locked into various positions for enhanced versatility.
Proper maintenance and understanding of these mechanisms can significantly impact the quality of your cuts. Regularly checking for wear and ensuring that all components function smoothly will lead to better performance and longevity of your equipment.
Base Support and Stability Features
The foundation of any cutting tool plays a crucial role in ensuring accuracy and safety during operation. A robust support structure is essential for minimizing vibrations and enhancing stability, allowing users to achieve precise cuts consistently. This section explores the key attributes that contribute to a solid base and their impact on overall performance.
Sturdy Construction: A well-designed support system is typically constructed from durable materials, providing resistance to wear and tear. This durability ensures longevity and reliable operation, which is vital for both professional and hobbyist users.
Adjustable Feet: Many models feature adjustable feet, which allow for leveling the equipment on uneven surfaces. This adaptability ensures that the tool remains stable, even in less-than-ideal conditions, promoting user safety and accuracy.
Non-Slip Base: A non-slip surface is integral for preventing movement during use. By incorporating materials that enhance grip, the tool remains securely in place, further reducing the risk of accidents and ensuring consistent performance.
Weight Distribution: Proper weight distribution is essential for balance. A well-engineered design ensures that the weight is evenly spread across the base, which aids in maintaining stability during operation and minimizes the risk of tipping over.
In summary, the combination of sturdy construction, adjustable features, non-slip surfaces, and effective weight distribution creates a reliable support system that enhances performance and safety, making the cutting experience more efficient and enjoyable.
Mitigating Wear on Moving Parts
Ensuring the longevity of mechanical components is crucial for maintaining optimal performance and efficiency. Regular maintenance and proper handling can significantly reduce the wear and tear that occurs over time, ultimately extending the lifespan of these essential elements. By understanding common causes of degradation and implementing preventive measures, users can achieve smoother operation and enhance reliability.
One effective approach to minimizing wear involves routine inspections and adjustments. Identifying issues early on can prevent minor problems from escalating into major failures. Additionally, the use of appropriate lubricants plays a vital role in reducing friction, which is a primary contributor to wear. Keeping components clean and free from debris is also essential, as contaminants can exacerbate wear rates.
Maintenance Task |
Frequency |
Benefits |
Lubricate moving components |
Monthly |
Reduces friction and wear |
Inspect for damage or misalignment |
Biweekly |
Prevents failures and prolongs life |
Clean surfaces and parts |
Weekly |
Removes debris and contaminants |
Check tension on belts and chains |
Monthly |
Ensures proper operation |
Implementing these best practices can significantly mitigate wear on moving elements, ensuring a higher level of performance and reliability. By investing time in maintenance and care, users can enjoy the benefits of improved efficiency and reduced operational costs.
|