Fuel Chamber |
Acts as a reservoir,
Internal Mechanisms and How They Operate
The intricate structure of these mechanical systems plays a crucial role in ensuring smooth operation and reliability. Inside, numerous components work in unison, creating a seamless flow of movement that powers the entire unit. Each element contributes to the precise function of the whole assembly, maintaining efficiency and consistency.
Key elements within the core system are responsible for controlling various processes, adjusting the output to match specific demands. These mechanisms constantly interact, regulating the flow of energy to achieve optimal performance under varying conditions.
Understanding how these components interact reveals the complexity of the design, highlighting the sophisticated engineering that makes it all possible. The careful balance and timing of the internal processes are essential for maintaining stability and ensuring the longevity of the system.
Key Functional Parts Overview
This section provides an insight into the essential components that work together to ensure the smooth operation of the system. Each element plays a vital role in maintaining functionality and reliability, with a focus on how they contribute to the overall mechanism’s performance.
- Main Control Element: This component is responsible for managing the flow and distribution within the system, ensuring balanced and precise operation.
- Regulating Valve: A crucial part that adjusts the pressure and maintains consistency, playing a key role in ensuring smooth transitions and stable output.
- Distribution Gear: This section oversees the coordination and timing, allowing for synchronized movements and efficient performance across the system.
- Feedback Mechanism: A vital feature that provides real-time monitoring and adjustment, enabling the system to adapt to varying conditions and maintain optimal performance.
Each of these elements interacts closely, working in unison to ensure the overall system functions effectively, highlighting the importance of their interconnected roles.
Examining Fuel Distribution Elements
In this section, we delve into the intricate network responsible for the efficient distribution of fuel within the system. Understanding how fuel is managed and directed through the components ensures optimal performance and reliability.
- Explore the pathways that guide fuel from its source to the combustion chamber.
- Analyze the key elements involved in regulating the flow of fuel without compromising efficiency.
- Discuss the mechanisms that control the timing and volume of fuel delivery to meet engine demands.
- Examine the components responsible for ensuring a balanced and consistent supply of fuel throughout operation.
- Highlight the importance of maintaining these elements to sustain peak engine performance over time.
By scrutinizing the fuel distribution elements, we gain insight into the operational dynamics that optimize engine functionality and longevity.
Dissecting the Governor System in Detail
The governor system plays a critical role in managing and regulating engine performance. By maintaining consistent operation, this mechanism ensures that varying external conditions do not impact overall efficiency. The system balances speed and power delivery, optimizing the engine’s performance in diverse scenarios.
Core Functionality of the Governor
At the heart of the system is a component responsible for adjusting the engine’s behavior in response to load changes. As the engine faces variations in demand, this element automatically compensates, either increasing or reducing power output to maintain stability. This balancing act is key to ensuring smooth operation under different conditions.
Fine-Tuning for Stability
The system includes intricate adjustments to fine-tune the balance between speed and torque. Small internal mechanisms work together to detect even the slightest changes in engine load, allowing for immediate and precise control. The result is a more reliable and efficient engine, designed to perform consistently even in fluctuating environments.
Role of Seals and Gaskets in Performance
The efficiency and reliability of mechanical systems depend heavily on the integrity of their sealing components. These essential elements help maintain proper operation by preventing unwanted leaks and preserving the correct balance within the assembly. Without proper sealing, even the most sophisticated designs can experience issues, leading to reduced output and potential damage over time.
Seals and gaskets serve multiple critical functions in maintaining performance:
- Leak Prevention: They ensure that fluids or gases remain contained within the designated areas, preventing loss of pressure or contamination.
- Environmental Protection: By creating a barrier, they keep external contaminants from entering the system, which is vital for preserving the inner workings.
- Vibration Dampening: Some gaskets are designed to absorb vibrations, helping to protect delicate components and reduce wear over time.
- Heat Resistance: Certain seals are made to withstand high temperatures, ensuring that extreme conditions do not compromis
Exploring the Pump’s Timing Adjustments
Understanding the nuances of timing adjustments is crucial for optimizing the performance of fuel delivery mechanisms. These modifications play a significant role in ensuring that fuel is introduced at the precise moment for efficient combustion, thereby enhancing overall engine efficiency and power output.
Timing adjustments can significantly affect the operational dynamics of the fuel delivery system. By manipulating these settings, one can achieve improved fuel atomization, which contributes to better combustion efficiency. It is essential to monitor and adjust these parameters to align with the specific requirements of the engine and its operating conditions.
Implementing precise timing changes involves careful consideration of various factors, including engine load and speed. Fine-tuning these settings can lead to noticeable improvements in throttle response and reduced emissions. Therefore, a thorough understanding of how these adjustments interact with the system is vital for any technician aiming to enhance engine performance.
In practice, making these adjustments requires specific tools and a comprehensive understanding of the mechanism’s operational principles. Regular assessment and recalibration ensure optimal functionality and longevity of the system. Engaging with these modifications not only benefits performance but also contributes to the system’s overall reliability.
Material Choices and Durability of Parts
The selection of materials used in the construction of components plays a crucial role in determining their longevity and performance. High-quality materials contribute to the overall reliability and efficiency of the system, ensuring that it operates smoothly under various conditions. Understanding the properties of different substances allows manufacturers to create more resilient and efficient mechanisms.
Several factors influence the decision-making process when choosing materials, including resistance to wear, corrosion, and the ability to withstand high pressures and temperatures. Selecting the right combination of these characteristics can significantly enhance the durability and efficiency of the components.
Material |
Advantages |
Disadvantages |
Steel |
High strength, excellent wear resistance |
Prone to rusting if not properly treated |
Aluminum |
Lightweight, good corrosion resistance |
Lower strength compared to steel |
Composite Materials |
Lightweight, customizable properties |
Higher cost, complex manufacturing process |
Brass |
Good machinability, resistant to corrosion |
Lower strength than steel |
In summary, the careful selection of materials is vital for creating robust and efficient components. By understanding the strengths and weaknesses of various substances, manufacturers can enhance the performance and durability of their products, ultimately leading to greater satisfaction for users.
Connection Points and Their Functions
This section explores the various connection locations within the system and their specific roles. Understanding these points is essential for ensuring optimal performance and functionality, as they facilitate the transfer of fluids and control signals necessary for the overall operation.
Key Connection Locations
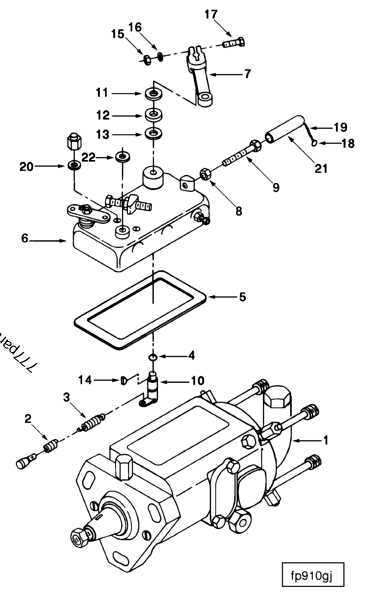
Connection Location |
Function |
Fuel Inlet |
Provides access for fuel to enter the mechanism, ensuring a steady flow for combustion processes. |
Delivery Outlet |
Directs the treated fluid to the combustion chamber, playing a crucial role in the efficiency of the operation. |
Return Line |
Allows excess fluid to flow back into the reservoir, maintaining optimal levels and preventing overpressure. |
Timing Control |
Regulates the timing of fluid delivery, which is vital for maintaining synchronization with the engine’s cycle. |
Importance of Each Connection
Each connection point serves a distinct purpose that contributes to the system’s reliability and efficiency. By ensuring that these locations are well-maintained and functioning correctly, users can enhance the overall performance and longevity of the entire assembly.
Signs of Wear in Critical Components
Identifying deterioration in essential elements is crucial for maintaining optimal performance. Regular inspections can help detect subtle changes that may indicate potential issues. Recognizing these signs early can prevent more severe complications and enhance the longevity of the system.
Here are some common indicators of wear:
- Unusual Noises: Listen for any irregular sounds, such as grinding or knocking, which may signal component failure.
- Decreased Performance: A noticeable drop in efficiency or power output can suggest that key parts are not functioning as intended.
- Visual Damage: Look for signs of physical wear, such as cracks, fraying, or discoloration on the surfaces of critical elements.
- Leaks: Fluid escaping from connections or seals can indicate a loss of integrity, requiring immediate attention.
- Inconsistent Functioning: Erratic operation or intermittent issues can point to failing components needing evaluation.
Addressing these signs promptly can help maintain the overall efficiency and reliability of the system, ensuring smooth operation and minimizing downtime.
Maintenance Tips for Optimal Efficiency
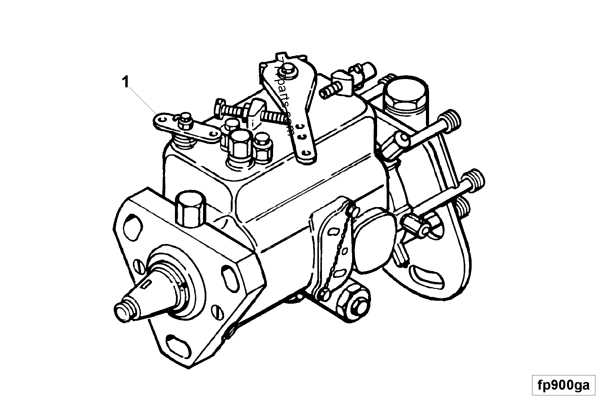
Ensuring the longevity and peak performance of your fuel delivery system is essential for smooth operation. Regular care and attention can help prevent costly repairs and maintain efficiency. Below are some practical suggestions to keep your system running optimally.
Regular Inspection
- Perform visual checks for any signs of wear or leakage.
- Monitor performance indicators to detect any anomalies.
- Inspect the seals and gaskets for signs of deterioration.
Fluid Management
- Ensure the use of high-quality fuel to minimize impurities.
- Change the fuel filter regularly to prevent blockages.
- Keep the system clean by draining any accumulated sediment periodically.
By following these simple maintenance tips, you can enhance the reliability and efficiency of your fuel delivery mechanism, ensuring optimal functionality for years to come.
Interchangeable Parts and Their Uses
The concept of interchangeable components plays a crucial role in enhancing the functionality and efficiency of various mechanical systems. By utilizing compatible elements from different models, users can improve performance and reduce maintenance costs. This flexibility not only supports repairs but also fosters innovation in design and engineering.
Benefits of Using Compatible Components
Integrating interchangeable components offers several advantages. It simplifies the repair process, as technicians can easily source alternatives. Furthermore, the ability to mix and match elements allows for greater customization of machinery to meet specific operational needs. This approach can lead to enhanced durability and reliability, ultimately benefiting end-users.
Commonly Interchanged Elements
Many elements within mechanical assemblies can be swapped out, provided they meet the necessary specifications. Below is a table highlighting some frequently interchanged components and their typical applications:
Component Type |
Common Applications |
Notes |
Seals |
Fluid containment in various systems |
Ensure compatibility with fluid types |
Gaskets |
Prevent leaks in assemblies |
Material choice affects durability |
Valves |
Control flow in hydraulic systems |
Matching pressure ratings is essential |
Pistons |
Provide motion in various machines |
Dimensions must be closely matched |
|