Eng
Electrical Connections in Meyer Plows
The wiring in specialized clearing equipment plays a critical role in ensuring efficient operation and control. Proper connection of all electrical components is essential to maintaining functionality, from powering the hydraulic system to controlling lights and signals. Understanding the basic layout of these connections can help in troubleshooting and maintaining smooth operation during intensive use.
The system typically includes multiple relays, switches, and a control module that work together to manage the equipment’s electrical flow. The wiring must be carefully routed to avoid interference and ensure a reliable connection, especially in demanding environments.
Special attention should be given to grounding and isolating the various components to prevent issues caused by vibration or exposure to moisture. Proper sealing and protection of wires is also necessary to extend the lifespan of the equipment and reduce the need for frequent repairs.
Mounting and Frame Assembly Details
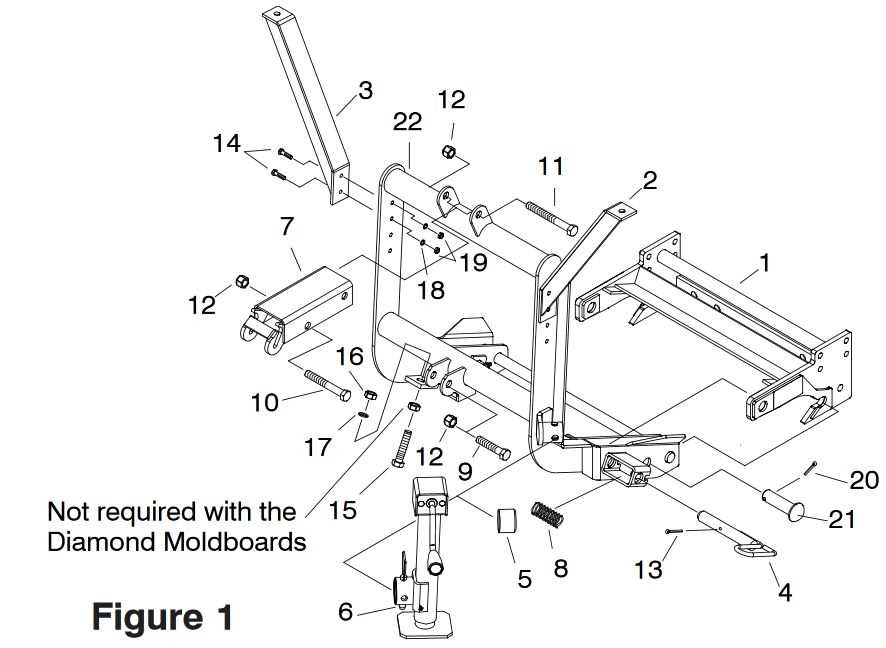
The assembly and installation of the mounting structure are critical for ensuring stability and functionality in various applications. Understanding the configuration and components involved allows for a seamless integration of the system with the vehicle. Proper attention to detail during the setup process can enhance performance and extend the longevity of the equipment.
Initially, it is essential to gather all necessary components and tools before starting the assembly. This includes brackets, bolts, and any other hardware specified in the assembly instructions. Each piece plays a vital role in providing a secure fit and should be inspected for any signs of damage or wear prior to installation.
The mounting framework is designed to be adaptable, accommodating various vehicle types. When aligning the frame, ensure that it is level and securely attached to the chassis. This alignment is crucial for optimal performance and prevents undue stress on the assembly during operation.
After securing the main frame, it is advisable to check all connections for tightness and stability. Any loose hardware can lead to malfunction or increased wear. Periodic maintenance and inspections should be conducted to ensure all components remain in good condition and properly secured.
Controls and Operating Mechanisms
This section delves into the various control systems and operating mechanisms essential for efficient functionality. Understanding these components is crucial for ensuring proper handling and effective performance of the equipment.
Key elements involved in the operation include:
- Control Levers: These are utilized to direct movements and actions, providing the operator with precise command over the machinery.
- Hydraulic Systems: These mechanisms facilitate the lifting and lowering functions, allowing for quick adjustments as needed.
- Electrical Controls: This includes switches and buttons that manage power distribution and operational settings.
Additionally, familiarity with the following aspects enhances the overall user experience:
- Operator Interface: The layout of controls should be intuitive for ease of use.
- Feedback Systems: Indicators that provide real-time information regarding the operational status can improve safety and efficiency.
- Maintenance Accessibility: Well-designed components allow for easy access during servicing, ensuring longevity and reliability.
In summary, a comprehensive understanding of the control and operating mechanisms is vital for optimal performance and user safety.
Maintenance Tips for Optimal Performance
Regular upkeep is essential to ensure that equipment functions efficiently and reliably. By following a few simple practices, users can extend the lifespan of their machinery while enhancing its effectiveness during operation. Consistent care not only prevents unexpected breakdowns but also contributes to smoother performance overall.
Start by inspecting components for wear and tear, as identifying issues early can save time and resources in the long run. Clean all surfaces to prevent the buildup of debris, which can hinder functionality. Additionally, lubricating moving parts regularly is crucial for reducing friction and wear, ensuring that each element operates harmoniously.
It’s also advisable to review and tighten all fasteners periodically. Loose bolts can lead to misalignment and further complications, negatively impacting the overall performance. Keeping an eye on fluid levels is essential too; ensuring that hydraulic fluids and oils are at appropriate levels will help maintain optimal operation.
Finally, always refer to the manufacturer’s guidelines for specific maintenance recommendations. Following these instructions can provide valuable insights tailored to the particular type of machinery, ensuring that it remains in peak condition for many years to come.
Identifying Wear and Tear on Parts
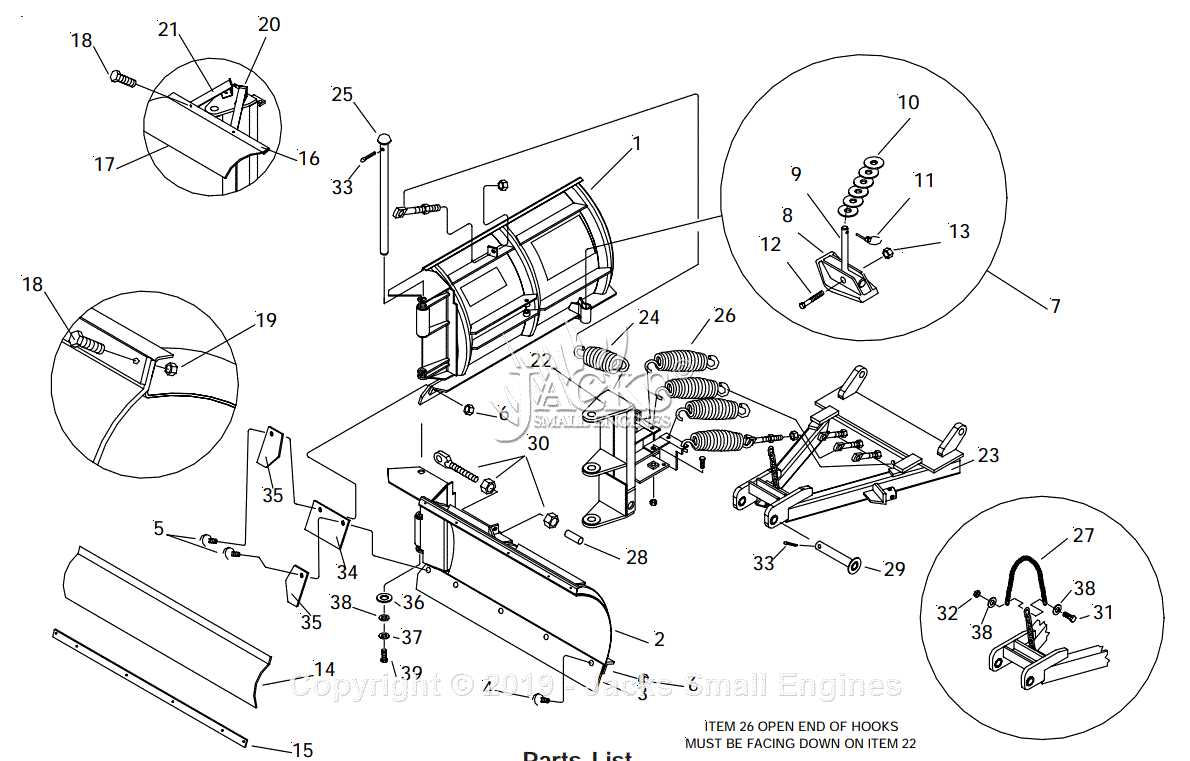
Over time, various components can show signs of deterioration due to frequent usage and exposure to harsh conditions. Recognizing these indications early can help avoid more severe damage and extend the lifespan of the equipment. Paying attention to specific areas that are prone to wear is crucial for maintaining efficiency and ensuring smooth operation.
Visual Inspections: Regularly checking for visible cracks, rust, or deformation can reveal the first signs of strain. Surface irregularities, even minor ones, can signal that more serious issues might develop if not addressed promptly.
Unusual Sounds or Movements: If the machinery starts making odd noises or operating less smoothly than usual, it could indicate internal wear that isn’t immediately visible. Listen for grinding, squeaking, or vibrations that were not present before, as these could point
Troubleshooting Common Issues
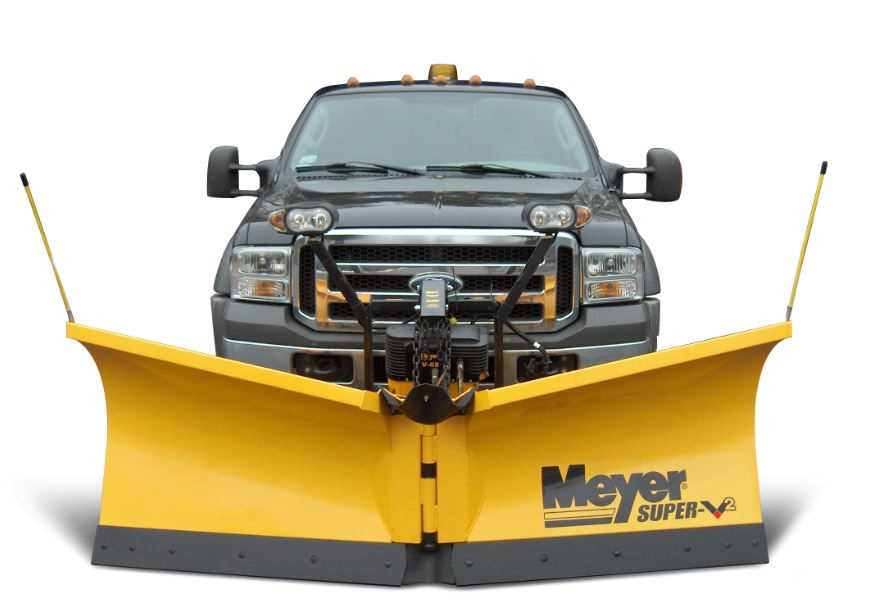
When dealing with equipment operation challenges, it’s essential to identify and resolve common malfunctions effectively. Understanding the typical problems that may arise can significantly enhance the functionality and longevity of the machinery.
Here are some frequent issues and their potential solutions:
- Hydraulic Problems:
- Inspect hydraulic fluid levels regularly to ensure optimal performance.
- Check for leaks in hoses and connections to prevent pressure loss.
- Replace any worn or damaged seals to maintain hydraulic efficiency.
- Electrical Failures:
- Examine all wiring and connections for signs of corrosion or damage.
- Test the battery and connections to ensure proper power supply.
- Replace any blown fuses to restore electrical functionality.
- Mechanical Issues:
- Inspect moving parts for wear and tear, lubricating as necessary.
- Check for proper alignment of components to prevent binding.
- Tighten loose bolts and fasteners to secure the assembly.
By following these guidelines, operators can effectively address and resolve common equipment issues, ensuring reliable performance throughout the operational season.
Replacement Parts and Compatibility Guide
This section provides essential information on alternative components and their compatibility within specific systems. Understanding the variety of options available ensures that users can maintain and enhance their equipment effectively.
When considering replacements, it is important to take into account several factors:
- Compatibility: Ensure that any component matches the specifications of the existing system.
- Quality: Opt for high-quality alternatives to ensure durability and optimal performance.
- Manufacturer Recommendations: Follow guidelines provided by the original manufacturer for the best results.
- Installation Requirements: Review any installation instructions to avoid complications during the replacement process.
Here are some common alternatives and their uses:
- Blades: Different shapes and sizes for varied applications.
- Hydraulic Components: Essential for effective operation and control.
- Electrical Systems: Includes wiring and connectors critical for functionality.
- Mounting Equipment: Ensures secure attachment to vehicles or machinery.
Consulting a professional or referring to detailed guides can further assist in selecting the right components for your needs.
Choosing the Right Plow for Your Vehicle
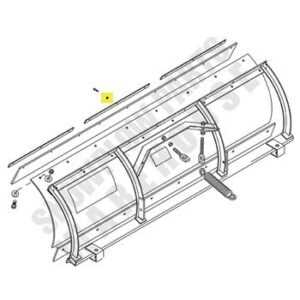
Selecting an appropriate attachment for your vehicle is crucial for efficient handling of challenging weather conditions. It is essential to consider various factors, such as the type of vehicle, the anticipated workload, and the specific environmental circumstances you may encounter. By understanding these elements, you can make a more informed decision that enhances performance and safety.
Assessing Vehicle Compatibility
Before making a choice, evaluate the compatibility of your vehicle with the attachment you intend to use. Different vehicles have unique specifications and limitations, which can significantly influence the efficiency of the attachment. Ensure that the weight, mounting system, and overall design of the equipment align with your vehicle’s capabilities.
Understanding Usage Requirements
Another critical aspect is to assess your usage needs. Determine how often you plan to use the equipment and in what conditions. If you anticipate tackling heavier or more challenging tasks regularly, selecting a robust and durable model will be advantageous. Additionally, consider features that enhance functionality, such as adjustable angles and additional accessories that improve performance.
Proper Storage Techniques for Meyer Plows

Ensuring the longevity and efficiency of your winter equipment requires proper handling and storage techniques. By following specific guidelines, you can protect these essential tools from environmental factors and mechanical wear. The right approach to storage not only maximizes their lifespan but also ensures they are ready for use when the season demands it.
Preparation Before Storage
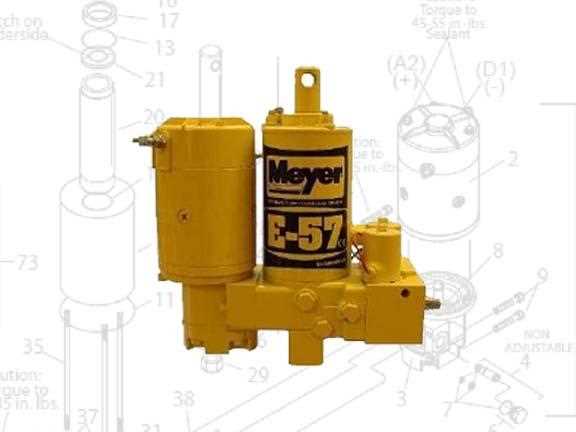
Before placing the equipment in storage, it is crucial to perform a thorough inspection and maintenance check. Clean any debris or residue that may have accumulated during use, as this can lead to rust or corrosion over time. Additionally, lubricate moving parts and check for any signs of wear that may require repairs. Proper maintenance is essential for maintaining functionality and performance.
Ideal Storage Conditions
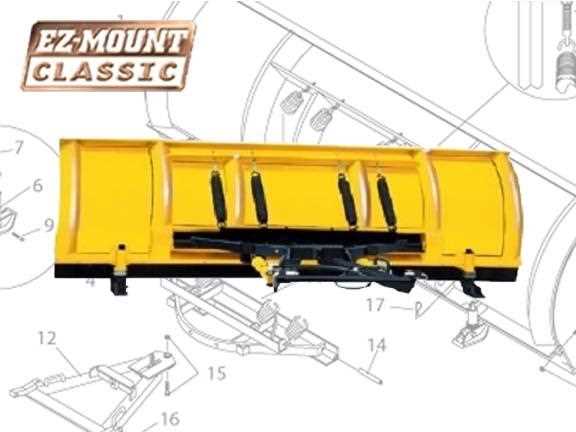
When choosing a storage location, opt for a dry and sheltered environment. Avoid exposing the equipment to direct sunlight or extreme temperature fluctuations, as these conditions can cause materials to degrade. Using protective covers can also help shield the equipment from dust and moisture, ensuring that it remains in optimal condition for future use.