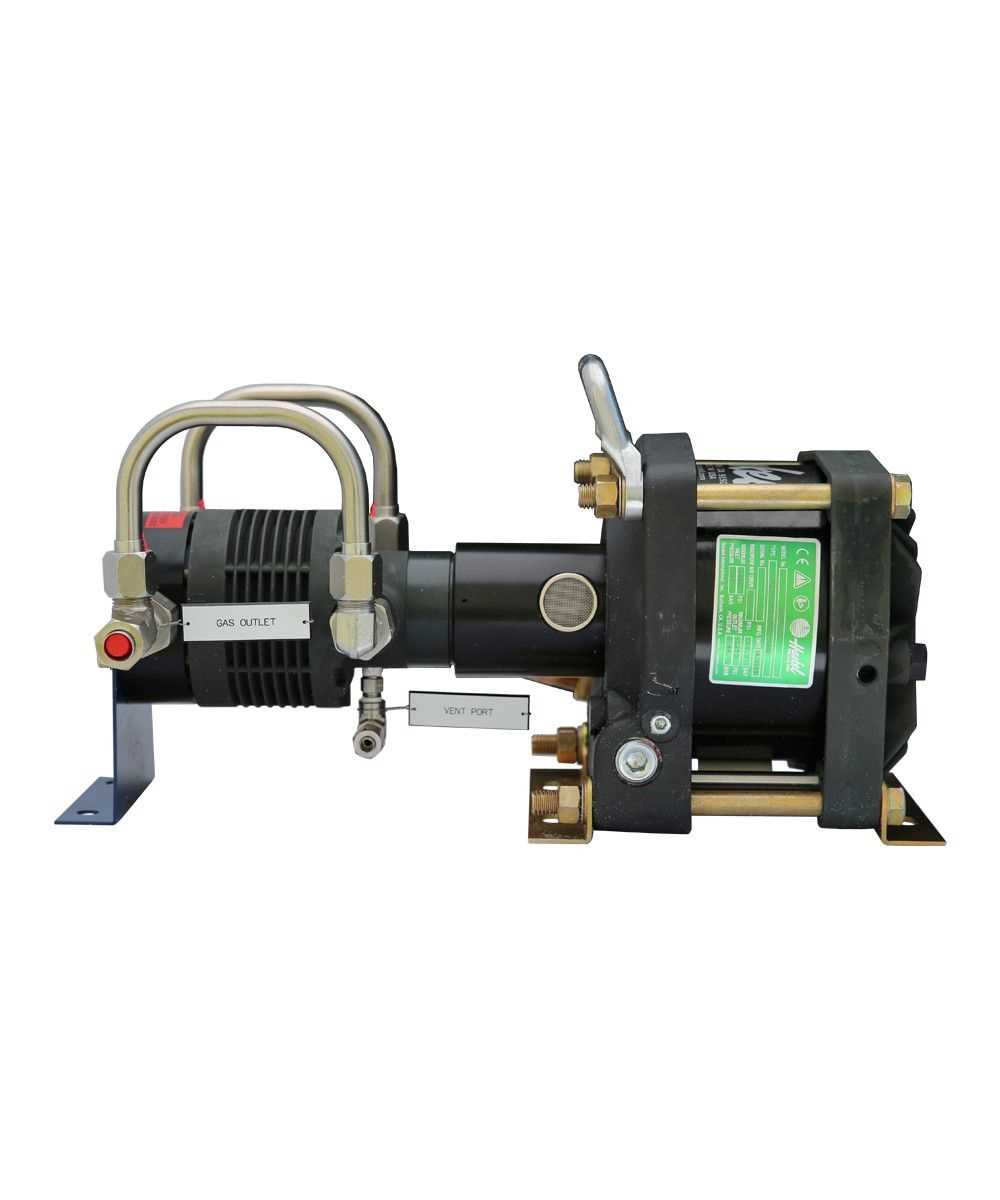
The intricate world of fluid dynamics relies heavily on a range of components that work harmoniously to achieve efficient operation. Grasping the various elements involved is crucial for anyone seeking to delve into the mechanics of these systems. A comprehensive overview allows for better troubleshooting, maintenance, and enhancement of overall performance.
To fully appreciate the functionality of these mechanisms, one must familiarize themselves with the various segments that contribute to their operation. Each element plays a specific role, influencing not only the efficiency but also the longevity of the entire assembly. Recognizing how these components interconnect offers invaluable insights into their collective performance.
Through detailed visual representations, understanding the layout and interaction of these essential parts becomes more accessible. Such illustrations provide a clear framework, enabling users to identify and differentiate between the various sections and their respective functions. This knowledge is instrumental for both novice enthusiasts and seasoned professionals in the field.
Understanding Haskel Pump Functionality
In the realm of high-pressure systems, the mechanics at play are crucial for efficiency and reliability. This section delves into the essential principles governing the operation of these devices, emphasizing how various components interact to achieve optimal performance. A solid grasp of these fundamentals is vital for effective maintenance and troubleshooting.
At the core of this machinery lies a mechanism that converts mechanical energy into fluid dynamics. The intricacies of this conversion process are what enable the system to achieve significant pressure levels. Precision engineering ensures that each element is finely tuned, allowing for seamless operation under demanding conditions.
Additionally, the functionality is influenced by the design of the chamber, which plays a pivotal role in the compression and transfer of fluids. Understanding the role of valves and seals within this setup is essential, as they regulate flow and prevent leaks, thereby maintaining system integrity.
Moreover, the interaction between the drive system and the fluid chamber cannot be overlooked. This synergy determines the efficiency and response time of the entire assembly, highlighting the importance of regular inspection and maintenance to uphold performance standards.
In summary, a comprehensive understanding of these operational principles not only aids in effective usage but also enhances the longevity of the device, ensuring it meets the rigorous demands of various applications.
Components of Haskel Pumps Explained
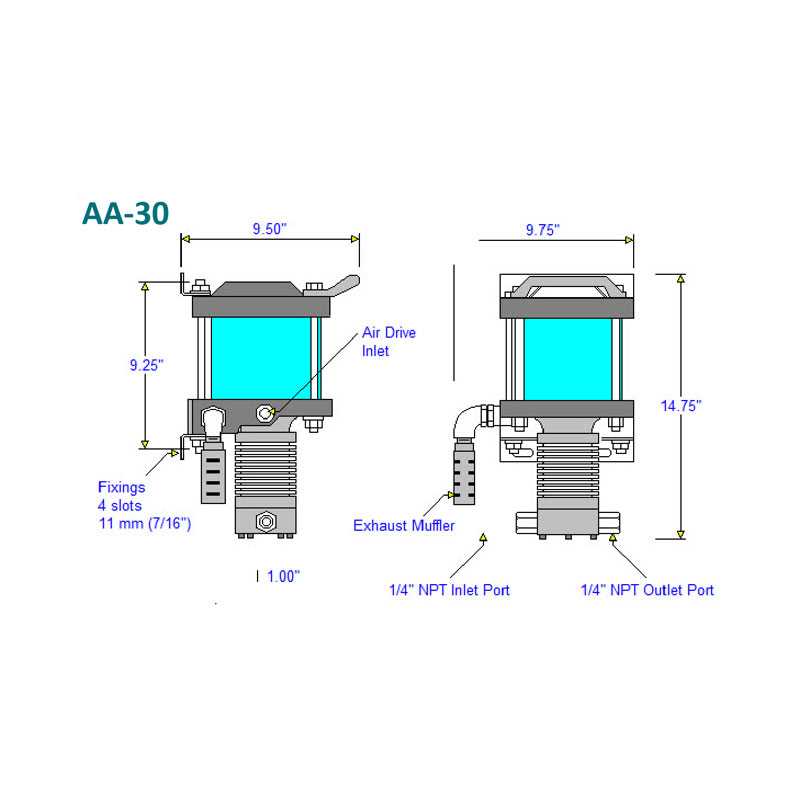
Fluid-driven machinery operates through a complex combination of key elements designed to maximize efficiency and durability. These elements work together to control pressure, manage flow, and ensure reliability in demanding environments. Understanding the role of each component is essential to maintain optimal performance and minimize wear over time.
Pressure Control Mechanisms
At the heart of the system lies the pressure regulation unit, responsible for managing the balance of force. This part ensures that the equipment can handle both low and high pressures without failure. Strong seals and valves are crucial here, as they prevent leaks and ensure a steady flow.
Importance of Accurate Diagrams
Having precise and detailed schematics is essential for ensuring the proper functioning and longevity of complex systems. When every component is clearly identified, it becomes easier to understand the overall structure and maintain efficiency in operation. High-quality illustrations prevent errors during maintenance and troubleshooting, ultimately saving time and resources.
Below is a table that highlights the key benefits of using precise illustrations in technical maintenance:
Benefit |
Description |
Clarity |
Helps to quickly identify each element and its position within the system. |
Efficiency
Common Issues with Pump Parts
Operational components can encounter a variety of challenges that affect performance and efficiency. These challenges often arise from wear and tear, improper maintenance, or external factors such as environmental conditions. Addressing these issues early can prevent larger failures and costly repairs.
Wear and Tear of Mechanical Elements
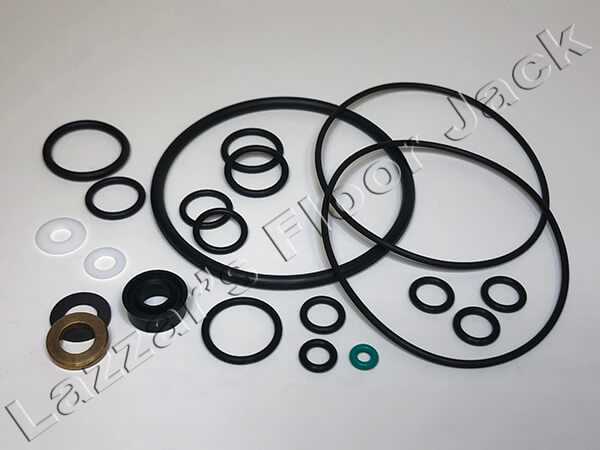
Mechanical elements are prone to deterioration over time, leading to reduced efficiency and potential breakdowns. Key components may experience friction, leading to overheating, which can cause further degradation. Regular inspection and timely replacement of worn-out elements are essential to ensure optimal functioning.
Seal and Valve Malfunctions
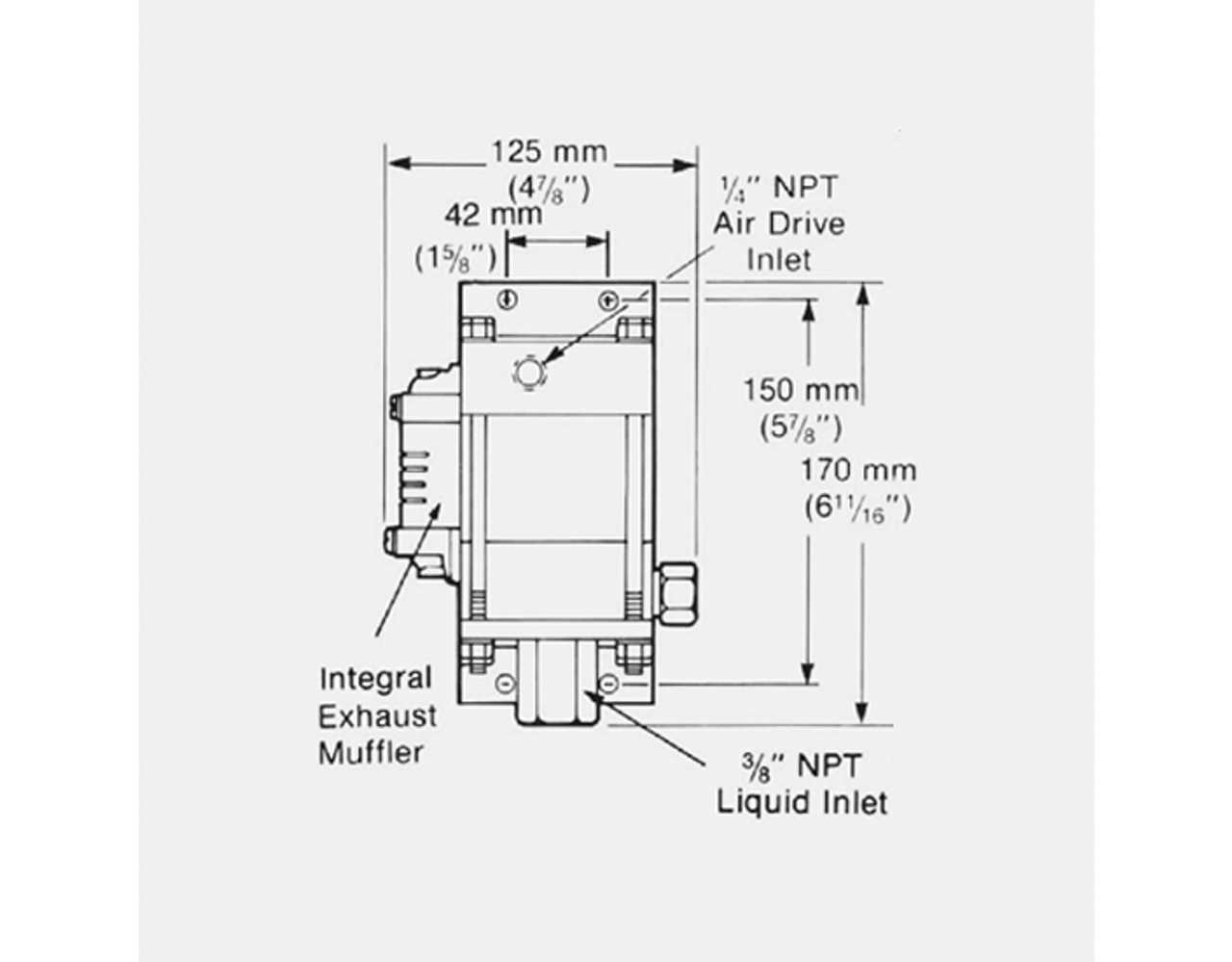
Seals and valves are critical in maintaining pressure and fluid control. Over time, seals can degrade or
How to Read Pump Diagrams
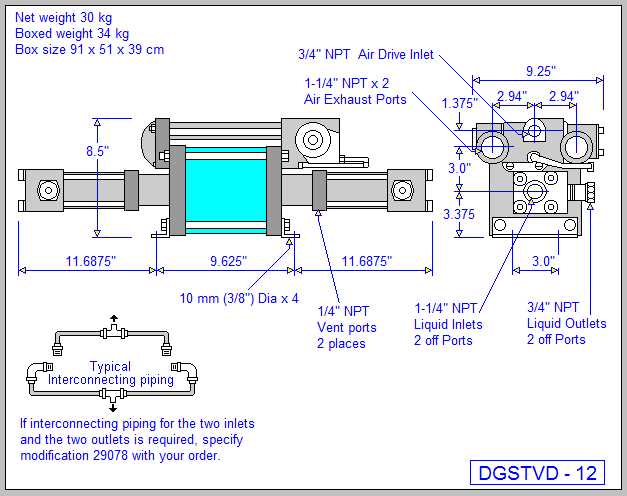
Understanding technical schematics is crucial for anyone working with mechanical systems. These illustrations display the structure and interconnections of components, allowing users to comprehend how everything functions together. A well-drawn schematic provides clarity on the flow of energy or fluid, making it easier to troubleshoot issues and perform maintenance.
The following table outlines common elements found in such schematics, and their typical representations:
Element |
Symbol |
Description |
Valves |
▲ |
Regulate the flow of liquids or gases in the system.
Maintaining Equipment Effectively
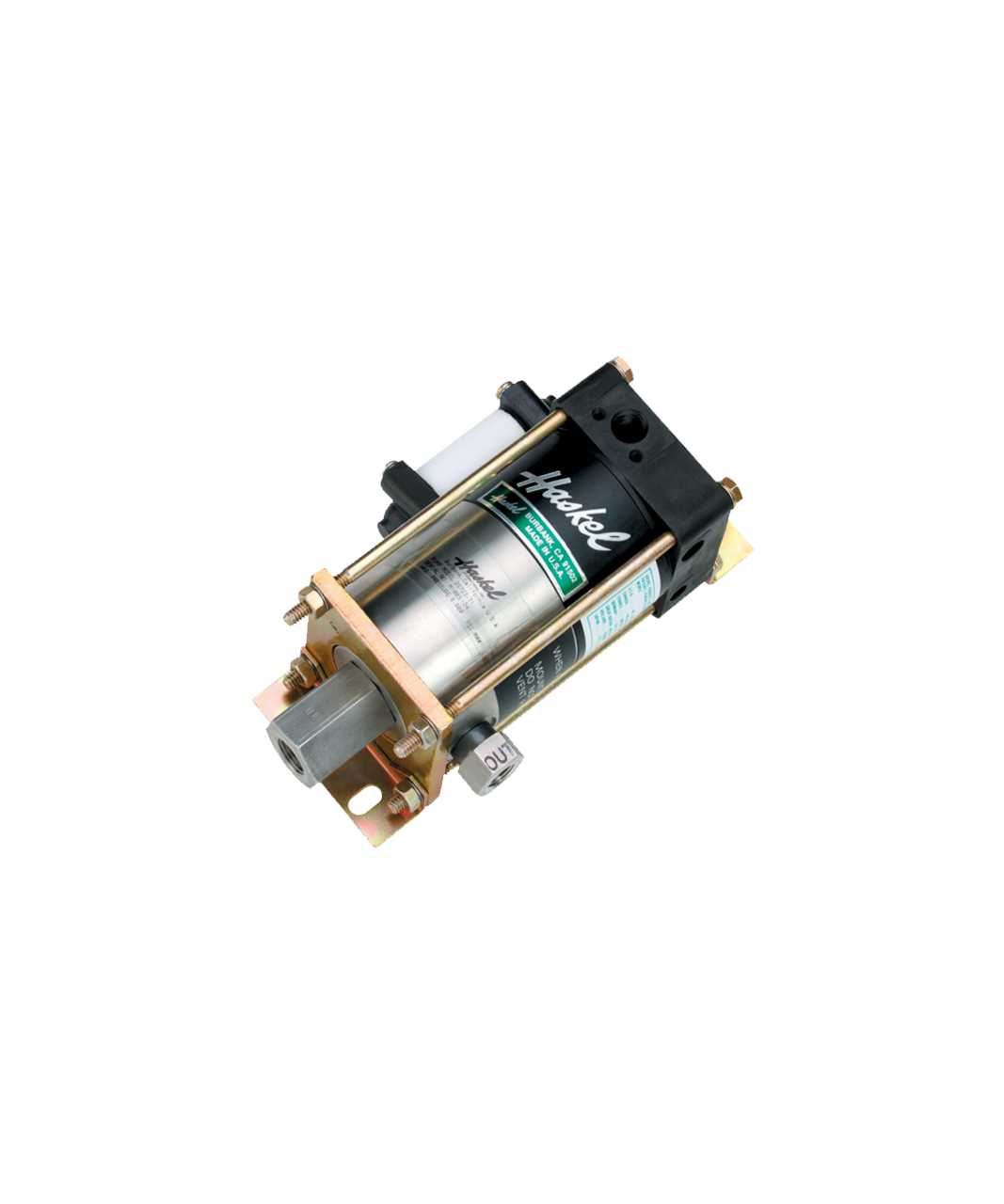
Proper upkeep of complex mechanical systems is essential to ensure their longevity and optimal performance. Regular inspections and preventive measures help to avoid costly repairs and downtime. By following a consistent maintenance schedule, operators can extend the lifespan of the equipment while ensuring safe operation in demanding environments.
Key Maintenance Steps
- Inspect components for wear or damage regularly.
- Ensure all connections are secure and free of leaks.
- Lubricate moving parts as recommended by the manufacturer.
- Replace filters and other consumables at the prescribed intervals.
Preventive Care Practices
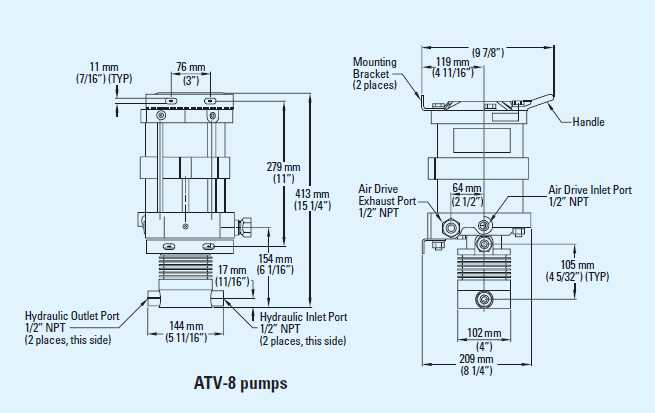
Preventive care is vital to avoiding unexpected malfunctions. By closely monitoring system performance, any signs
Identifying Wear and Tear Signs
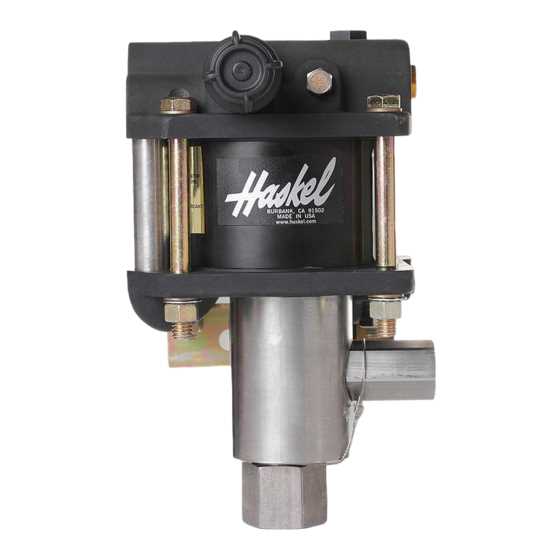
Recognizing the early signs of wear is essential to maintaining the longevity of mechanical equipment. By paying attention to subtle changes, it’s possible to prevent more serious issues and reduce downtime.
- Increased noise levels: A sudden rise in operational noise often indicates internal components are struggling due to wear.
- Reduced efficiency: Noticeable drops in performance can be a sign that some elements are not functioning as smoothly as they should.
- Visible damage: Cracks, dents, or other physical defects on key surfaces may suggest advanced wear and should be addressed immediately.
- Frequent overheating: If the equipment consistently runs hotter than usual, it could point
Upgrading Parts for Improved Performance
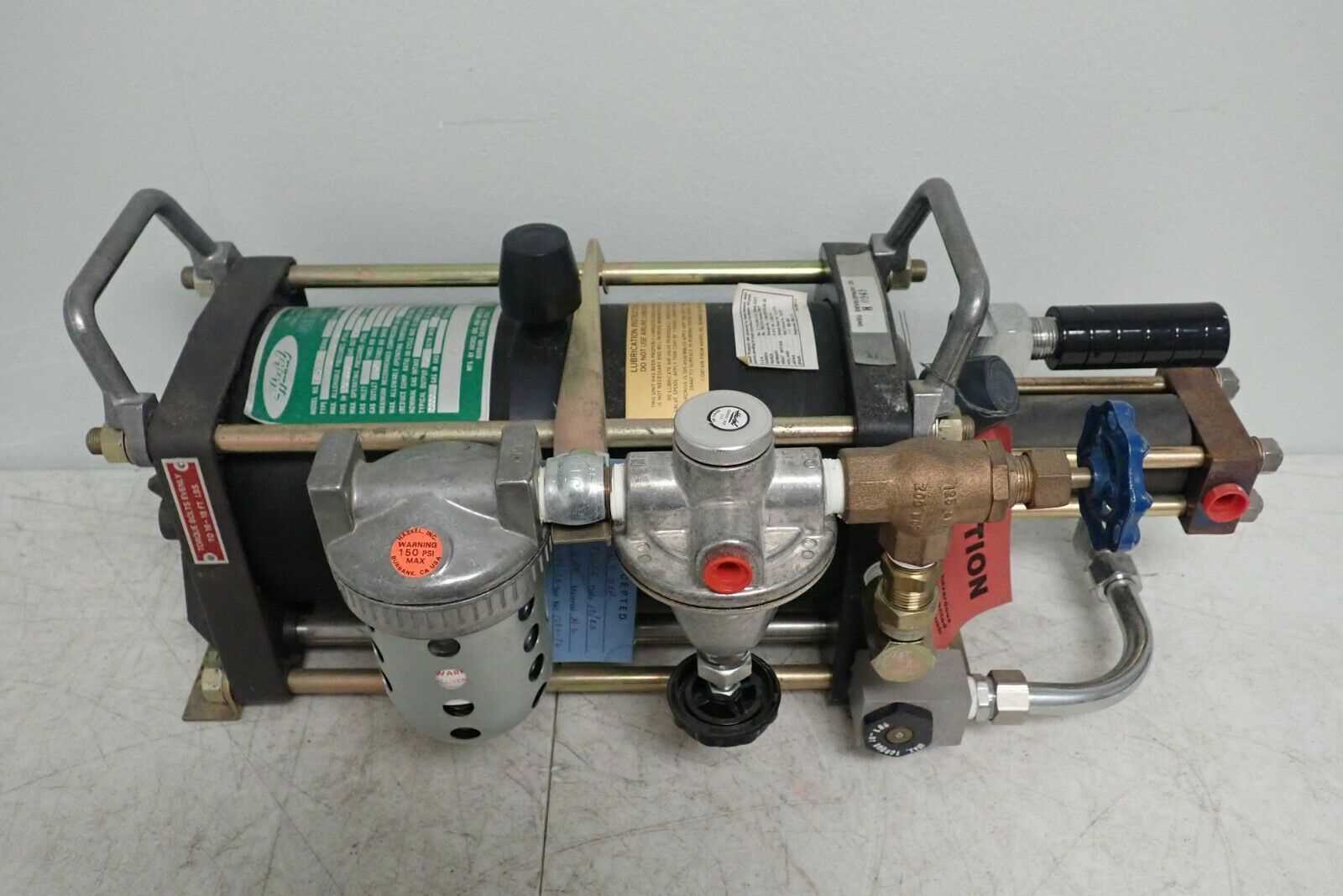
Enhancing the efficiency and reliability of mechanical systems often involves replacing certain components with upgraded alternatives. This process helps optimize overall functionality, reduce wear, and extend the system’s lifespan. When selecting new elements, it’s important to focus on durability and compatibility to ensure a smooth upgrade process.
Material Considerations
Choosing higher-quality materials for critical elements can significantly improve performance. For instance, components made from advanced alloys or composites tend to last longer and offer better resistance to corrosion and extreme conditions
Haskel Pump Safety Precautions
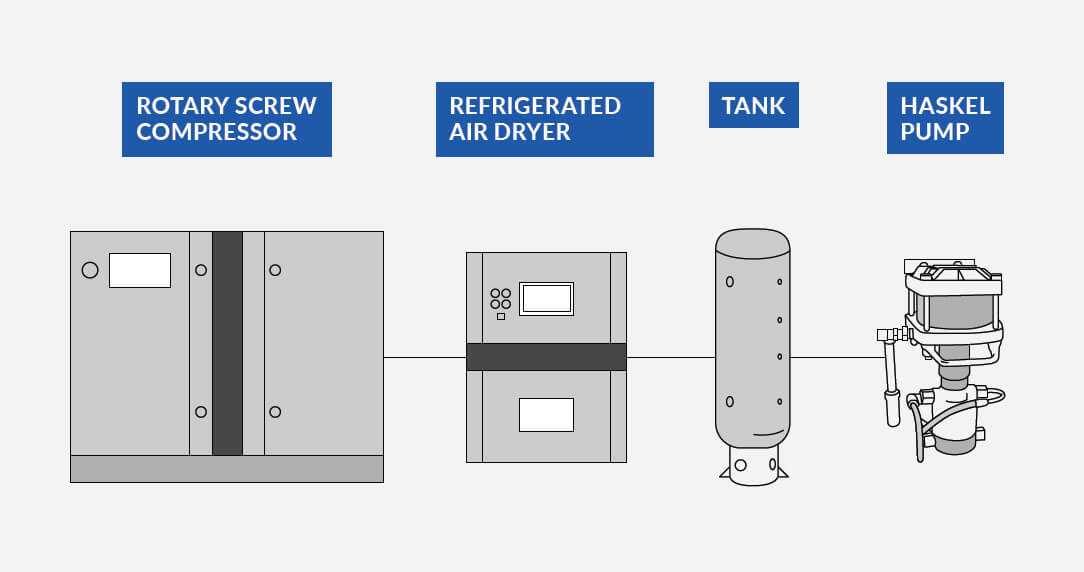
When working with high-pressure equipment, it is crucial to prioritize the safety of all personnel and ensure that proper guidelines are followed. Adhering to safety standards minimizes risks and helps avoid potential hazards during operation. Regular checks, proper handling, and awareness of surrounding conditions are essential for maintaining a safe environment.
Regular Inspections: It is important to conduct routine inspections to detect wear, leaks, or other issues that may compromise the reliability of the system. Early detection can prevent more serious problems.
Proper Training: Operators should be thoroughly trained to understand the equipment and its safe usage. This includes familiarizing themselves with all c
Difference Between Haskel Models
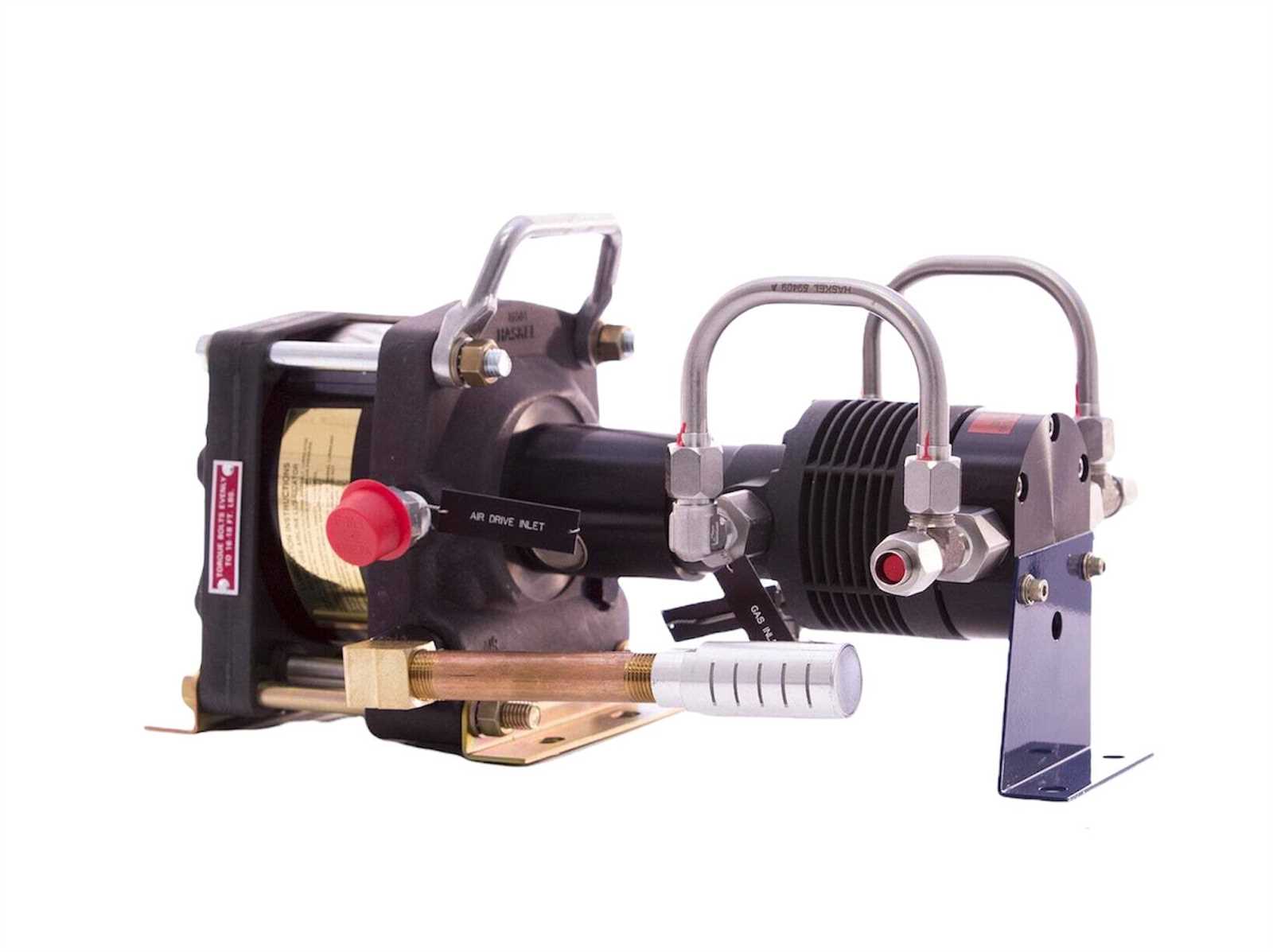
When exploring various designs within this category of fluid transfer systems, it’s crucial to recognize the distinctions in functionality, efficiency, and applications. Each variant is tailored to meet specific operational requirements, offering unique benefits that cater to diverse industrial needs.
The first model typically emphasizes higher flow rates, making it suitable for applications requiring rapid fluid movement. In contrast, another design might prioritize pressure stability, ensuring consistent delivery even under varying conditions. Additionally, some iterations are engineered for portability, providing a lightweight solution ideal for mobile operations.
Furthermore, variations in materials used in construction can affect durability and resistance to corrosive environments. For instance, certain models are crafted with advanced alloys, enhancing their longevity in harsh settings. Overall, understanding these differences enables users to select the most appropriate system for their specific tasks, optimizing performance and efficiency.
Choosing the Right Replacement Parts
Selecting appropriate components for machinery is essential for maintaining optimal performance and extending its lifespan. A thoughtful approach to replacement can prevent future issues and enhance overall efficiency. Understanding the specific requirements of the device and the characteristics of various alternatives is crucial for making informed decisions.
When evaluating options, consider factors such as compatibility, durability, and performance specifications. Here is a table that outlines some key considerations for choosing suitable replacements:
Factor |
Description |
Compatibility |
Ensure the replacement matches the specifications of the existing components. |
Material Quality |
Look for high-quality materials that offer longevity and resistance to wear. |
Performance |
Consider the operational efficiency and how the replacement will impact the overall functionality. |
Manufacturer Reputation |
Research the reputation of the manufacturer to ensure reliability and support. |
Haskel Pump Assembly Instructions
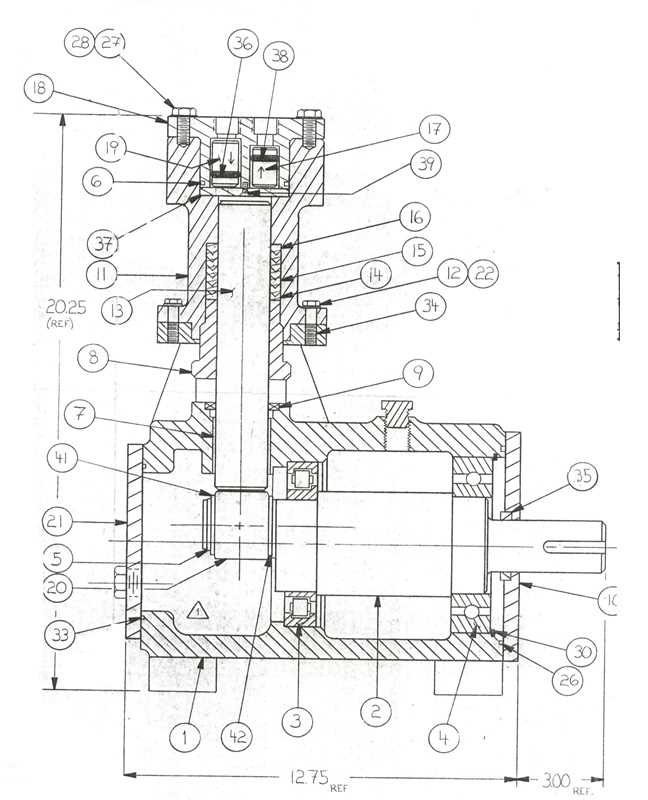
This section provides a comprehensive guide for the assembly process of a specific fluid transfer device. Following these instructions will ensure proper setup and functionality, leading to optimal performance in various applications.
Required Tools and Materials
- Wrench set
- Screwdriver
- Sealant or lubricant
- Instruction manual
- Safety goggles
Step-by-Step Assembly Process
- Begin by laying out all components on a clean surface.
- Refer to the instruction manual for the specific sequence of assembly.
- Attach the main housing by aligning it with the base.
- Secure all connections tightly using the appropriate wrench size.
- Apply sealant to prevent leaks where necessary.
- Double-check all bolts and fittings for tightness.
- Perform a final inspection to ensure all parts are correctly assembled.
|
|